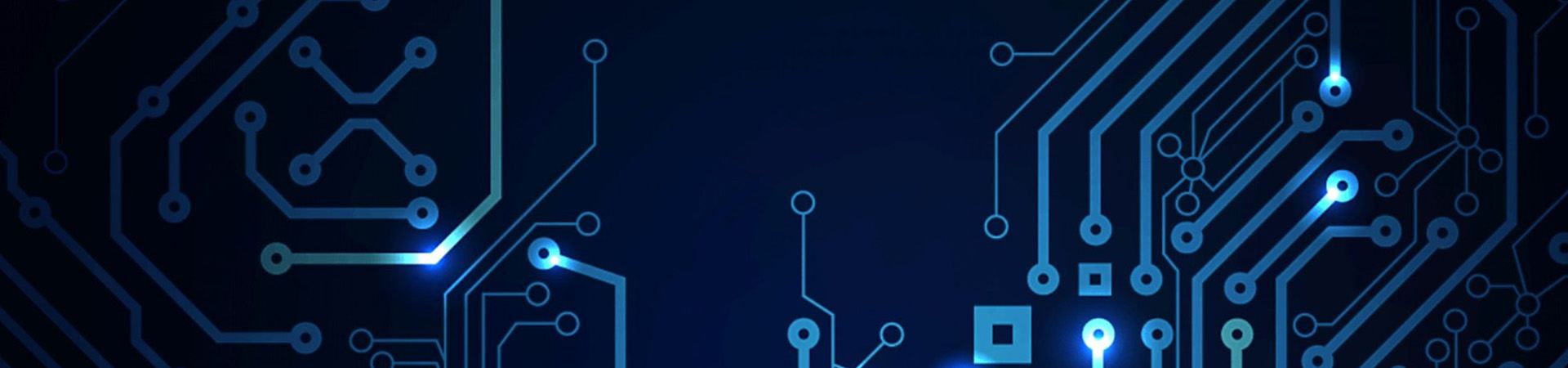
PCB Manufacturing Process
What is the PCB ?
A Printed Circuit Board (PCB) is a thin board made of fiber, composite epoxy, or other laminate material. The PCB connects all the other components inside, so you can use your electronic device for what it is intended to do.
Basic PCB Manufacturing Process Step by Step
Step 1: Data Preparation
Once we receive Gerber data from the customer, we send to CAD department, we check customer data meets our manufacturing requirements. These checks are mostly done automatically. We check the track widths, the space between tracks, the pads around the holes, the smallest hole size etc. The engineer can also check and measure individual areas where he wishes. Once the data is verified as good, he will output all the tool files needed to drive the machines that will make and test the PCB.
Step 2: Plotter
We use laser photo plotters in a temperature and humidity-controlled darkroom to make the films. The photoplotter takes the board data and converts it into a pixel image. A laser writes this onto the film. The exposed film is automatically developed and unloaded for the operator. The films are ready now for the PCB fabrication process. Once we generate films for each PCB layer. The operator will arrange them so that they are properly aligned. The operator puts the film on the table of the punch and then micro-adjusts the table until the targets on the film are exactly lined up with the targets on the film punch. The operator then punches each sheet of film with the registration holes which will fit onto the registration pins in our imaging equipment.
Shearing:
Laminates are sheared as per the specifications given in the job cards and transferred into panel form if it is single and double board it will go directly in the drilling process, for multi-layer board first we have to develop inner layers.
Step 3: Print inner layers for multilayer PCB
We use a glass epoxy laminate material to produce inner layer for our multi-layer PCBs, the operator loads first inner layer print on panel board the printer uses powerful UV lamps which harden the photoresist through the clear film to define the copper pattern. Under the black areas, the resist remains unhardened. The clean room uses yellow lighting as the photoresist is sensitive to UV light.
Outside the yellow room, the panel is sprayed with a powerful alkali solution which removes the unhardened resist (etching) . The panel is pressure-washed and dried. The operator checks a sample of the panels to make sure that the copper surface is clean, and all the unwanted resist has been removed. You can now see in the blue resist what will be the copper on our inner layer panel in PCB Manufacturing Process.
Etch inner layers
We remove the unwanted copper using a powerful alkaline solution to dissolve (or etch away) the exposed copper from the inner layer. The process is carefully controlled to ensure that the finished conductor widths are exactly as designed. But designers should be aware that thicker copper foils need wider spaces between the tracks. The operator checks carefully that all the unwanted copper has been etched away
Next, we strip off the blue photoresist which protected the copper image. So now we have the exact pattern required. The operator checks that all the photoresist has been removed. You can see that we put several different designs on one production panel. That way we can make small numbers of PCBs cost-effectively.
Inspection of inner layers in PCB production
- The inner core of our multilayer is now complete. Next, we punch the registration holes we will use to align the inner layers to the outer layers. The operator loads the core into the optical punch which lines up the registration targets in the copper pattern and punches the registration holes.
- We won’t be able to correct any mistakes on the inner layers once we have assembled the multilayer, so we now give the panel a complete machine inspection.
- The automatic optical inspection system scans the board in broad strips and compares it with the digital image generated from the original design data. Any errors are displayed on screen.
Lay-up and bond
- The outer layers of our multilayer consist of sheets of glass cloth pre-impregnated with uncured epoxy resin (prepreg) and a thin copper foil.
- The lay-up operator has already placed a copper foil and 2 sheets of prepreg on the heavy steel baseplate. Now he places the pre-treated core carefully over the alignment pins. Then he adds 2 more sheets of prepreg, another copper foil and an aluminum press plate.
- He builds up 3 panels on the baseplate in the same way. Then he rolls the heavy stack under a press which lowers down the steel top plate. He pins the stack together and rolls the finished stack out of the clean room into a rack.
- The press operator collects 3 stacks on a loader and loads them into the bonding press. This press uses heated press plates and pressure to bond the layers of the PCB together. The heat melts and cures the epoxy resin in the prepreg while the pressure bonds the PCB together. The process is computer controlled to build up the heat and the pressure correctly, hold it and then to cool the press down. In this way we ensure a permanent bond that will last the lifetime of the PCB. Our board has 4 layers but complex PCBs for defence, avionic and telecommunications applications can have more than 50. These may include sub-assemblies of cores, prepregs and foils drilled and plated before being assembled into the final PCB.
- Once the cycle is completed the press operator unloads the press and carefully rolls the heavy stacks into the clean room. Here the lay-up operator de-pins the stack and removes the top plate. He unloads each of the panels from the stack, removing the aluminum press plates used to ensure a smooth copper finish. The copper foil is now bonded in place to form the outer layers of the PCB.
Drilling printed circuit boards
Holes are drilled in the panel using a computer-controlled program generated from CAD output. The plated-through holes are used to provide paths for making electrical connections between PC board’s various layers. Some of these holes are also used as receptacles for mounting connector pins or other components on the PC board. Non-plated-through holes are used as attachment holes for mounting connectors to the PC board or attaching the board to the equipment in which it will be installed in PCB Manufacturing Process.
Step 4: Plating Through Holes
Copper is plated on holes by Electroless method to provide conductivity between all copper interfaces. Copper is plated by the chemical immersion process.
Step 5: Yellow Room
The panel is chemically cleaned and a layer of light-sensitive material (photo – resist) is applied to both sides. The resist layer is soft when applied to the panel surface but hardens when exposed to ultra – violet rays.
A photo-tool (film) with the circuit image required is placed over the resist layer. This is held down by a vacuum. The panel is then exposed to ultra-violet light. The dark area of the film protects the resist from the light and the resist stays soft. The clear area of the film lets the light penetrate through onto the resist and the resist hardens.
The panel is then passed through a developing process, which removes all the soft resist. Thus, the circuitry pattern in the resist develops away.
Step 6: Electro Plating
Electro Copper plating serves to build up the copper plating thickness both in the holes and on the required circuit area.
After the copper is plated, tin is plated over the surface of the copper. This protects the copper lines from etching when the resist is stripped off and the unwanted copper is etched away.
Step 7: Etching & Striping
The dry film is removed from tin plated panels and the exposed copper (not protected by tin) is etched away leaving the desired circuitry pattern. At this point, the fundamental circuitry of the board is completed
Step 8: Liquid Photo Imaginable
Photo Imaginable Solder Mask is used to protect the circuits from an environment. P.I.S.M. is coated onto the boards using screen printing method.
P.I.S.M. hardens when exposed to UV light. During exposure, a photo-tool is placed over the panel. The dark areas of the photo-tool prevent exposure of the P.I.S.M. on the copper pads.
After exposure, the panel is developed to wash away the unexposed solder mask. The mask is then cured.
Next, we apply solder mask area to the entire board, with the exception of solder pads. Solder mask prevents solder from accidentally shorting out any other parts of the printed circuit board. Later, when assembling the boards by attaching components, the solder should only adhere to designated solder pads.
Step 9: Nomenclature (Legend)
Legend is used to indicate the position of components on the circuit board. It is printed on the boards via a silk-screening process.
Step 10: Routing
The routing process is a milling process in which a routing bit is used to cut the profile of the desired board contour. The panels are “pinned and stacked” as previously done during the “Drill” process. The usual stack is 1 to 4 panels.
Last, but not least, we route the perimeter of the board using NC equipment. The board is now complete and is quickly shipped off to you — our happy customer!
Step 11: Electrical Testing
The purpose of an electrical test is to check the electrical integrity of the circuit, i.e.: to make sure that the circuits are complete and carry the correct currents. Using a test fixture, which consists of a series of pins, every circuit is tested. The pins are aligned with the features. Current is passed between one test point and a test point on the same track. If a signal is detected the circuit is okay.
Step 12: Final Inspection / Quality Control
A final inspection checks for visual defects and those that would not necessarily fail the Electrical Test. As a final check to ensure the product meets our customer’s standards, and prior to pack and ship, 100% quality audit is performed on board lots. whole PCB manufacturing process.