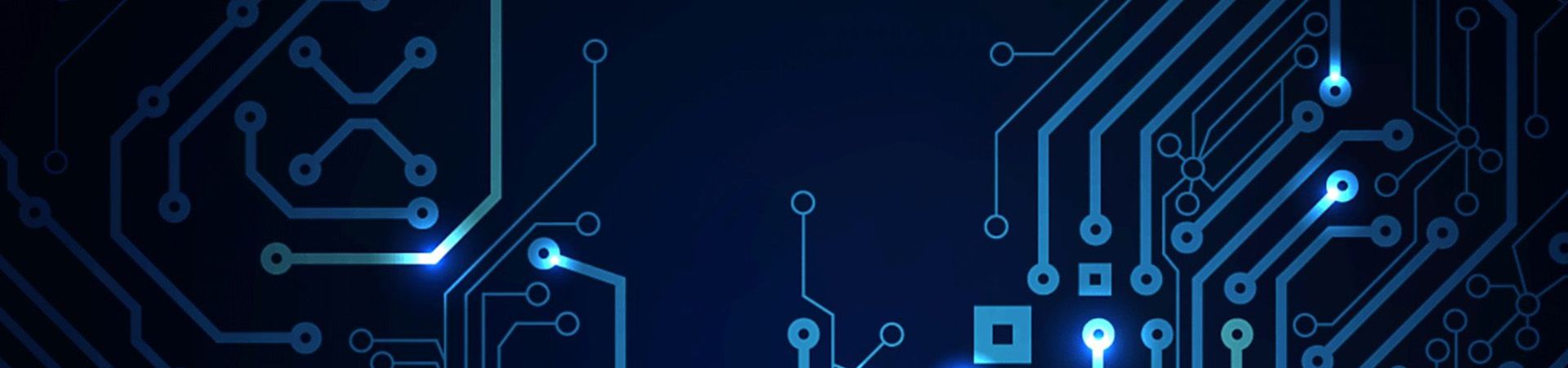
5 Best Practices to Build Efficient Bill of Materials
Bill of Materials (BOM) is generally considered one of the most essential aspects of data in the PCB assembly process. It includes a comprehensive list of electronic components required to be sourced for assembling a PCB.
With the right BOM, the manufacturing and assembly processes required to build PCB streamlines which invariably results in better efficiency and turnaround time for your projects. So let us explore what is the right way to build BOM for your workflows and ensure greater efficiency in your processes.
5 Constructive Practices To Create Highly Efficient BOMs
Creating BOMs in the right way can be highly beneficial for your overall process management. Here are some of the ways that you can use to build effective BOMs:
-
Leverage a Microsoft Excel Spreadsheet to Add Data Labels
Creating proper data labels for your BOM can streamline your project requirements and help you succeed in your projects. Below are the things that we suggest you include in your BOMs:
-
Item Number
Each type of part that you need for the project is assigned an item line or item number. Just note this number and if the item number is the same as the part number, you can simply note the quantity of the part.
-
Quantity
It is used to denote the number of specific parts you need per board.
-
Reference Designators
These are used to depict the parts on the PCB silk screen. Hence, you should place all the same part numbers in the same Excel spreadsheet cell and can also specify a contiguous range using a dash such as R2-R5.
-
Manufacturer Details
It is a good practice to include the component manufacturer’s name in your BOM to avoid any confusion at later stages.
-
Manufacturer Part Number
It is used to describe the part number you will use when the exact same part is brought from a distributor or manufacturer. Make sure to include all the suffixes with the number as a small change can lead to a big confusion.
-
Distributor Part Number
It may not be necessarily needed, but having it can solve any conflict that may arise during the process.
-
Description
It is the description of the product provided by the distributor or manufacturer. It includes value of the component.
Add a comprehensive and informative description of every part and material used within a BOM. This significantly aids you and others in identifying and differentiating between similar parts and materials.
-
Package
It is optional information that you can add to determine the standard package type and prevent redundancy.
-
Type
It indicates the generic type of the part or the common parts of a PCB like resistors, capacitors, etc., that can be easily replaced at the later stages of the PCB design process.
Having listed your project’s BOM can help eliminate any potential uncertainties and streamline your process for better efficiency and a faster assembly process.
-
-
Include BOM Part Numbers for All Listed Components
The Bill of Materials that you prepare must have a supplier part number and a manufacturing part number for all the listed components. Having these details help in ensuring the right documentation for your project and swiftly starting the assembling process of your PCB. In case you can supply the Digi-Key part number, then other information might not be required as it would cover the required details.
-
Add Do Not Place Label on Unnecessary Components
Oftentimes, confusion between the components may arise while placing them on your PCB board. Hence, to save yourself from trouble, make a practice of clearly labelling all the DNP parts on the BOM.
You can either highlight the DNP parts with red in the reference designator column or add them to the bottom of the BOM to make a distinction.
-
Utilise a Single Tab in Excel Spreadsheet for Your BOMs
It is recommended to leverage a single tab in your excel spreadsheet while constructing your BOMs. It will help you better understand what the buyers need and prevent any misinterpretations.
Also, this way cross-checking the components that you need in the project gets easier. Furthermore, you can order or source parts more quickly for the manufacturing and assembling process.
-
Use an Older Microsoft Excel Version for Unsuccessful File Exports
Oftentimes, the BOM import tool that you use is not able to successfully process the excel files in .xlsx format. This usually occurs when you build an Excel file using non-Microsoft applications such as Apple Numbers, Google Docs, or CAD tools.
In that case, use an older version of Microsoft Excel to export the file to solve the problem. If it still doesn’t work, just copy-paste the data into a new Excel file, save it, and then upload it with your BOM import tool.
Conclusion
BOM essentially serves as a blueprint for the entire product manufacturing and assembling process. Hence, it is vital to develop your BOMs effectively to streamline the PCB assembling process and save substantial time and effort. Apart from it, with the right BOMs, you can significantly improve communication and eliminate redundancies and errors.