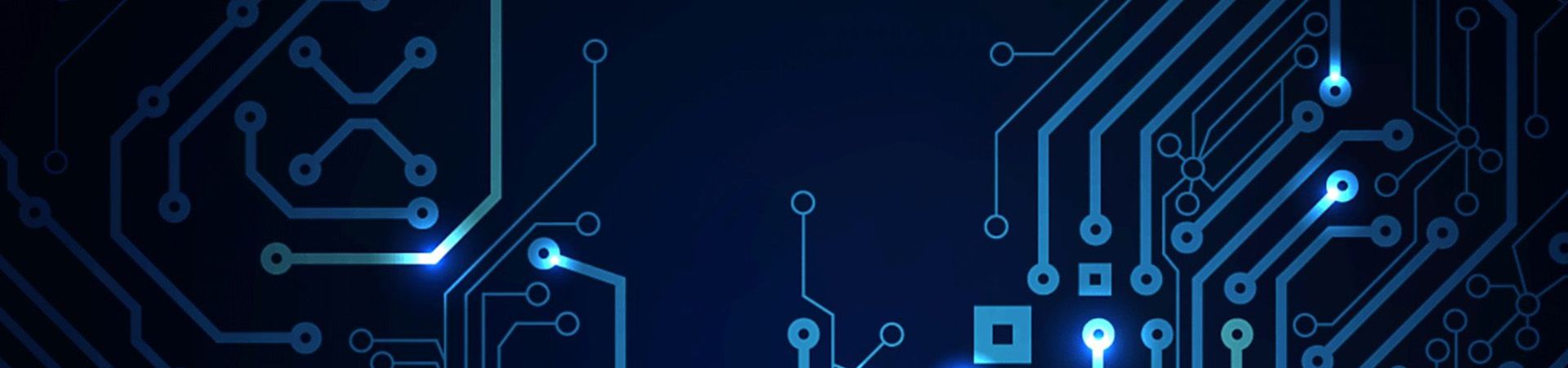
Streamline all your PCB orders
Ecommerce has made it possible to place orders online without having to go through a rigorous process of inviting quotes, going through product brochures, and making manual comparisons. Instead, now you can easily add inputs, select the preferred materials, and add the mechanical dimensions to place the order for a custom solution.
While it has become easier to order electronics components online, it does not mean you can eliminate the rigor required to vet all the data before you send it out to place the order. Online order placement works on the same adage - garbage in, garbage out. If you cannot provide accurate data for the order, you should expect delays since there will be some back & forth between you and your manufacturing partner before you can finalize all the necessary details.
If getting your order processed and delivered on time is a crucial priority for you and your team, ensure that you provide accurate data and purchase specs while placing an order. Over the years, as the preferred turnkey manufacturing partner for electronics components, we have experienced consistent gaps between required input data package benchmarks and the data we receive.
Nearly a third of exceptions are raised based on this required and received data disparity. Here are the seven standard exceptions our team has observed over the years.
7 Common Exceptions While Ordering PCBs Online
PCB Layer Mismatch
One of the most common mismatches we keep receiving is the gap between the layers mentioned in the order specs and those available in the files we receive. Think about it this way - you place an order for a 4-layered PCB and then provide the data package for a 2-layer PCB.
Such data packages are fundamentally lagging behind the required order information. A two-layer PCB will need the top and bottom circuit details. In contrast, a four-layer PCB would require two layers for the inner circuits and the top and the bottom circuits.
Solder Mask Disparity
It is common for buyers to consider and order two sides of solder masking. However, many times, despite placing the order, their sent data package has one side of the solder mask missing from all considerations. Even if you focus only on the through-hole components, our quality assurance experts highly recommend solder masks on the top and the bottom sides of the PCB.
The Case of Excessive Information
Yes - this can be a real challenge. Many customers place orders and omit the option of adding silk screens which act as legends on their PCBs. Then, they sent us the comprehensive input data package - with silkscreens. Ideally, we would recommend customers use silkscreen in their PCBs. But, if their design does not have room for such details, they can avoid it. We recommend such customers not send out additional and unnecessary data. Such data files slow down the process since the team working on the order has to flag exceptions to resolve confusion, which adds to the delivery timeline.
Missing Gerber Data
If you have chosen to add special technological features and functionalities like Via Filled, Carbon, Peelable, Countersunk, and Serialization, your input data files must include the Gerber layers for these add-on features. Such files help our team determine which side of the PCB should get the additional features.
Dimensional Disparity
Another standard error is the gap between the ordered thickness and the mechanical layer-defined thickness. We have observed customers ordering PCBs with a thickness of 1.6 mm and then providing input files that establish the mechanical layer at 2.4 mm.
In addition to the very thickness of the PCB, customers should also define the stack-up process. Customers often order standard layer stack up and then send the input data package requiring custom stack up configurations.
The same disparity also exists in the way customers set the copper thickness for their PCBs. All these disparities add up to the delivery time and make the eventual delivery more expensive.
Material Conflicts
Our team conducts a comprehensive assessment of the material TG requirements. We assess the data files, mechanical drawings, and readme files to determine any visibly erroneous conflicts in the ordered and the briefed material preferences.
Impedance
Impedances can be challenging from a PCB design and engineering standpoint. Hence, if your design requires impedance, we strongly recommend you to provide the following details:
- Signal Layer and Reference Layer
- Track Width and Transmission Line Spacing
- Copper Thickness
- Dielectric Thickness
- Impedance Value
This checklist is for your due consideration. Once you have submitted the data files, our team calculates the impedance to ensure your provided data and our material availability are in perfect sync with your requirements. If we find any discrepancies, we immediately raise an exception and recommend the solutions to remediate them.
In Summary
We strongly recommend that customers send the Gerber layers alongside the data package, order specs, and other critical information for the PCB manufacturing process. We provide a free design for manufacturability check at the beginning of the process to ensure you and our team are on the same page regarding your design's viability and its fit with the use case you are targeting.