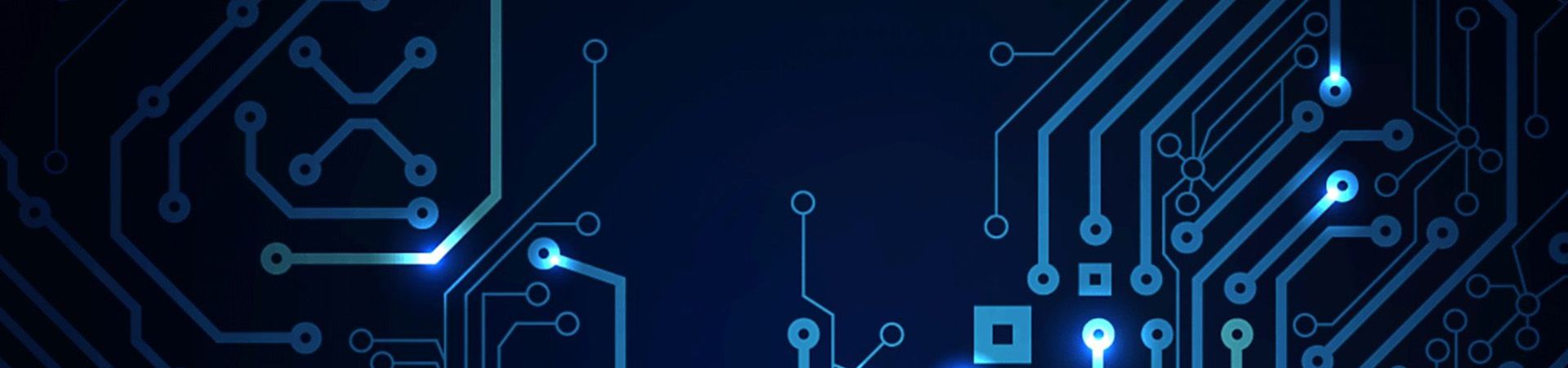
Defining PTH and NPTH in PCB Circuit Design — PCB Power Market India
At PCB Power Market, circuit board manufacturing involves drilling holes into or through a copper-clad insulating substrate and etching the copper foil to form a specific circuit. Depending on the functional requirement, the holes in multilayer printed circuit boards may be vias, plated through holes (PTH), or non-plated through holes (NPTH). While vias and PTH have a thin barrel of copper along their wall, NPTH do not. The difference between vias and PTH is that PTH holes span the entire thickness of the board, while the depth of via holes are limited to one or two layers at the most. Circuit board fabrication with through-hole technology uses a process of electroless copper deposition to deposit the copper layer necessary to establish the conducting wall for vias and PTH.
Through Hole Technology
In PCB manufacturing and assembly, through-hole technology refers to a certain mounting scheme. In this scheme, assemblers use electronic components that sport long leads, which, in turn, require inserting into holes in circuit boards before soldering. Assemblers insert through-hole components either manually or by using automated insertion machines.
Initially, assemblers used the long leads of through-hole components to solder them in a point-to-point construction. With the advent of printed circuit boards, this was no longer necessary, as copper traces on the board provided the connections. It was enough to solder the leads to copper pads surrounding the holes, which, in turn, were part of the interconnecting copper traces.
With the progress to two-layered and then to multilayered boards, fabricators had to start plating the through holes to allow them to electrically link copper traces on the two outermost layers.
As technology progressed further, the introduction of surface mount components (SMT) made the through-hole technology redundant for mounting components. The design of leads on SMTs allow them to solder directly on copper pads on the board without requiring the drilling of any holes. The use of through-hole technology on SMT boards is now mainly as vias, and is mainly for interconnecting different layers. Some components, especially high power dissipating ones, connectors and wires, still require the use of PTH, mainly to provide them with mechanical mounting strength. The use of NPTH is mainly for non-electrical fittings, and machine mounting.
PCB fabrication requires a clear distinction between plated-through holes and non-plated through-holes. Designers must make this distinction during the PCB circuit design process. Manufacturers expect the PTH design to follow specific criteria for them to process the hole as a PTH, else, they will consider and process it as an NPTH.
Plated Through Hole (PTH)
A PTH will always have a copper pad on both the outermost layers, and both copper pads will continue up to the lip of the hole. Depending on the requirement, pads may also be present in the inner layers around the PTH, with the inner diameter of the pads equal to the diameter of the hole. This is an important criterion for all plated through holes, which ensures that once the electroplating process creates the copper barrel on the wall of the hole, it will electrically connect to all the pads.
To meet the above requirement during the PCB circuit design, the designer must generate a pad with a diameter a minimum of 12 mil larger than the hole diameter. This will leave a minimum pad width of 6 mil after drilling the hole. If the PTH is in the shape of a slot, the designer must create a pad that will leave a minimum width of 6 mil copper around the slot. Most PCB design tools will add a suitable solder stop mask to the generated pad.
Non Plated Through Hole (NPTH)
Unlike plated-through holes that must have a copper pad on the outermost layers, non-plated through holes may or may not have a copper pad surrounding the hole. Manufacturers will consider a hole as NPTH if:
- There is no copper pad surrounding the hole on the outermost layers.
- There is a copper pad surrounding the hole, but the inner diameter of the copper pad is at least 12 mil larger than the hole diameter. That means there is a clearance of at least 6 mil between the copper pad and the hole.
The above requirements ensure that the electroplating process will be unable to create any copper barrel on the wall of the hole, and the hole will therefore remain non-plated.
To meet the above requirement during the PCB circuit design, the designer must generate a pad equal to or somewhat smaller than the hole diameter. To avoid confusion, these pads must be free-floating, or remain unconnected to any other feature in the design. The PCB design tool adds a suitable solder stop mask to the pad. If the NPTH is meant for mounting a mechanical fixture, the designer must also allow sufficient clearance to the neighboring track or pad.
Comparing PTH and NPTH
During printed circuit board fabrication, the fabricator must drill all plated through-holes before starting the electroless copper plating process. This ensures the formation of the copper barrel on the hole wall in case of PTH. Since for NPTH, there is no requirement of a copper barrel in the hole wall, it is immaterial if the fabricator drills NPTH holes before or after the electroplating process.
The fabricator drills through holes that pass completely through the thickness of the PCB. For plated through holes, an electroplating process deposits a thin layer of copper on the walls of the holes, electrically linking all pads surrounding the hole. If the board has through-hole components, after assembly, solder will anchor component leads within the hole to the copper barrel. This ensures better mechanical stability, reliability, and lower resistance. For multilayered boards, PTH electrically connects inner layers as necessary to the outermost layers.
As there is no copper barrel in the hole wall of non-plated through holes, these holes are electrically non-conducting. Most of the NPTH in a PCB are mounting or tooling holes. They are necessary for fixing the PCB to its operational location, or for guiding the PCB when mounting it on a machine for some process. For single sided boards, all holes will necessarily be NPTH, with component leads passing through some.
With the advent of multilayer boards, and increasing use of surface mount technology, use of through holes, whether PTH or NPTH, is significantly decreasing.
Lowering Through Hole PCB Cost
Drilling a PCB is an added expense to the cost of the board. The final cost of the board depends on the number and size of the holes, the size of their annular rings, and the design of the holes. Here are some ideas to lower the cost of a printed circuit board with through holes:
- Use larger diameter holes — Drilling smaller holes is more expensive. Higher precision is necessary, and more frequent breakage of drill bits not only adds to the cost, but also to the fabrication time. Contacting the manufacturer is the best way to know the actual cost of a board with very small diameter holes. Most PCB suppliers add an upcharge for holes with diameters between 0.15 mm and 0.3 mm.
- Use large annular rings — A smaller annular ring around the hole requires more precision while drilling. If the drill centering is not precise, the annular ring may not remain homogeneous around the hole. Using a large annular ring overrides this concern. However, it reduces the space available for routing traces on the PCB, and this may require the PCB size to increase.
- Use lower hole density — Higher hole density means drilling more holes per square centimeter of the board. Apart from making the PCB mechanically weaker, the drilling time also increases. This has the effect of increasing the fabrication time, and hence, the cost of the PCB. Decreasing the hole density may reduce the printed circuit board price.
Conclusion
Although through-hole technology was once necessary for making multilayered boards, modern manufacturing techniques such as those practiced by PCB Power Market has reduced their use to a significant extent. Although printed circuit boards still have both plated through and non-plated through holes on them, specific use cases restrict their number.