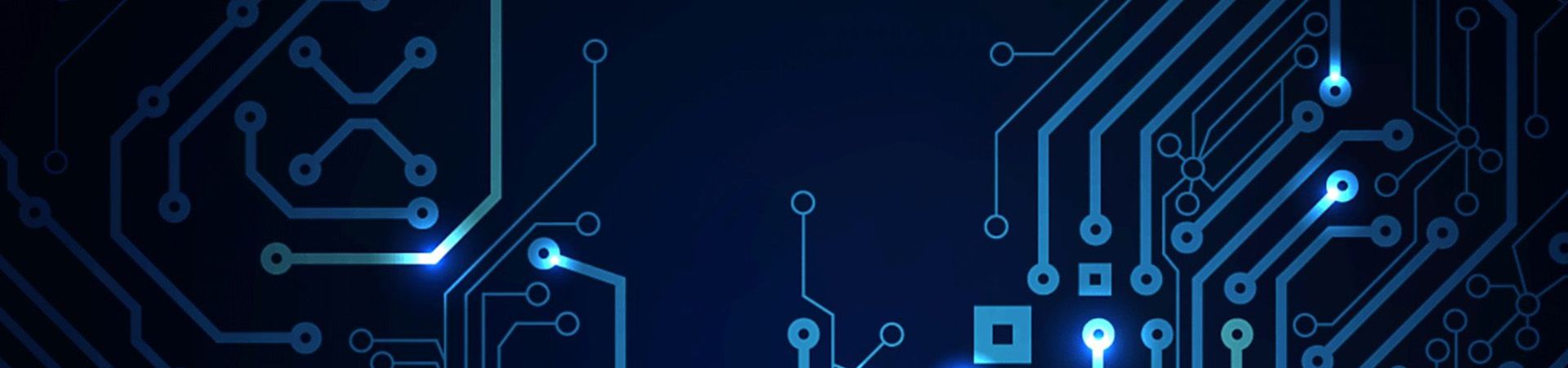
Everything You Wanted to Know About Automated Inspection Systems — India
The printed circuit board or PCB is equivalent to a central processing unit in any electronic product,it is important that it continues to function effectively. As technology advances, printed circuit boards are becoming smaller, more compact and more complicated. With the advent of surface mount or SMT components, the average circuit board now has several thousand solder joints and this is where the vast majority of problems begin.
As production volumes increase, it requires rigorous manual inspection. Engineers would need to examine each component in detail, assessing their alignment and qualifying their solder joints on the board. This would greatly increase the risk of missing many imperfections.
On the other hand, the increasing demand to manufacture and deliver large quantities of products to the market is becoming shorter and shorter. Original equipment manufacturers or OEMs need better and more reliable testing and inspection methods to ensure the quality of their products, and they need to be fast enough not to slow down the production process. This is where the automated optical inspection methods or AOI come into play.
What is Automated optical inspection?
In simple terms, AOI is the visual inspection of a circuit board at various stages of the PCB manufacturing process, both bare PCBs as well as PCBs occupied with electronic components.
PCB manufacturers perform a detailed scan of the board with a high-resolution camera to identify missing or bent components, soldering defects, shorts, and other quality defects. The system can illuminate the circuit board with LED, infrared, ultraviolet, and fluorescent light to capture multiple images. There are two main ways to program an AOI system.
Use a "golden board": If you use a good board, the images will form a standard against which all subsequent boards can be compared.
In subsequent production runs, the AOI system scans and compares each PCB board image to the gold standard and flags any differences found. Engineers then examine these differences in magnified views and determine if there are defects and identify effective ways to fix them.
Algorithm-Based Programming: The system accepts circuit board data and uses it to create your own profile for a board.
Advantages of Automated Optical Inspection
With AOI it is possible to indicate process issues at different stages of manufacturing, namely:
- Bare board fabrication
- Applying solder paste
- Assembly of SMT components
- Post soldering of SMT components
Feedback from AOI stations at each of the above stages helps troubleshoot problems by formulating a quick response to your query.
Detecting errors early in the manufacturing process helps to significantly reduce the cost of subsequent corrections. It also helps avoid the problem of the same errors recurring during high-throughput production, which could become costly and time-consuming.
Because AOI is a real-time process, this resulting data it generates helps improve the manufacturing process and its quality control. It also helps to quickly fix potential problems and reduce them to zero, improving large-scale production performance.
With effective algorithms, an AOI system can track and document defective boards and good boards. This improves process management efficiency, operational integrity, and traceability.
AOI devices can be easily customized, allowing manufacturers and assemblers to tune the system to effectively bypass acceptable circuit boards and block defective ones. In addition to removing surface defects, AOI systems also help reveal larger defects prior to electrical inspection. This is advantageous for data collection for statistical process control.
Considerations for Automated Optical Inspection
Although using AOI offers several advantages, it is necessary to maintain a high level ratio of the pass rate to the parameters. A high pass rate can mean that approved products are more likely to be reliable in their operation. However, a high success rate is not always an indication of a product's guaranteed performance.
Similarly, a low success rate does not always mean poor build quality. The low success rate could be an indicator of the specific standards that the manufacturer has implemented.
Therefore, the OEM should look for a high-performing end product rather than a high success rate.
As a rational approach the manufacturer should focus on the inspection parameters. This is important because the automated system simply responds to operator commands. The AOI system only checks what is requested and ignores those not specified by the operator. In general, using AOI during the PCB manufacturing stages ensures consistent and repeatable results.
Types of Automated Optical Inspection Methods
PCB manufacturers use several structural inspection technologies that account for different costs, performance and defects. These inspection technologies range from the simplest visual inspection methods to the most complex X-ray inspections. It is common in the industry to divide PCB assembly inspection technologies into two broad categories: manual visual inspection methods and automated optical test inspection methods.
Manual visual inspection methods
There are many steps in PCB assembly that benefit from visual inspection. Depending on the assembly stage, the fitters select the equipment for the visual inspection.
For example, a manual visual inspection immediately after solder paste printing can detect misalignment, partial printing, excess paste in small areas, solder paste in covered holes, and contaminated solder paste. However, since manual inspection can check about 5 connections per second, this method is only useful for small and medium volume production runs.
Automated optical inspection methods
As production volumes increase, so does the importance of accuracy and speed. In many cases it is also necessary to inspect hidden solder joints such as those found under BGAs, J-Lead devices and surface array flip chips. Because it is a high-density package, it must be inspected based on specially established uniform rules.
The industry uses digital equipment for automated real-time inspection and failure analysis. Digital equipment greatly improves the capacity and repeatability of these AOI systems.
Most AOI systems rely on some form of light emission: visible, laser, and X-ray light. The equipment collects data by processing, measuring, the image in real time and locating defects in components and their welded joints. Such automated optical inspection systems do not physically contact the circuit board. However, they are sophisticated enough to provide high repeatability while effectively removing subjectivity from the inspection process.
AOI systems use multiple visible light sources.
They use video cameras, programmable LEDs and computerized systems while inspecting welds. The intensity and curves of the light reflected from the welds provide information about the curvature of the welds. Analysis of the captured data helps determine solder joint integrity, solder amount, solder bridges, wetting, drift, and missing components.
AOI systems are suitable for inspecting 30-50 solder joints per second for devices with pitches greater than 20 MIL.
Automated optical inspection systems also use other methods in the industry, namely:
- Automated Laser Test Systems
- X-Ray Fluoroscopy Test Systems
- X-Ray lamination inspection systems
The inspection method mainly depends on the inspection speed, type of defects and associated costs.
Automated Laser Inspection Systems (ALT)
With ALT or automated laser inspection systems it is possible to measure shape and height deposits of solder paste. The system focuses a laser beam on the surface of the weld to measure its reflectivity and height by measuring the angle of reflection on multi-position detection detectors.
ALT systems help with gathering real-time information from the solder paste footprint, including orientation, viscosity, cleanliness, and other attributes.
X-ray fluoroscopy system
When the X-ray beam is passed vertically through the circuit board, the X-ray fluoroscopy test system generates a density image. This helps to closely inspect solder joints, assessing their thickness and internal integrity.
Digitizing the image helps in examining defects in the solder joints, such as B. Misalignment, presence of voids, bridges, insufficient amounts of solder and cracks.
X-ray inspection systems
The X-ray laminating system produces images of local planes of the horizontal section of a printed circuit board. These slice images typically have a surface thickness of 8-16 MIL and allow inspection of different sections of the same weld joint. The X-ray Lamination Test System is suitable for inspecting PTH or plating through holes and solder joints under BGA ICs.
Conclusion
The printed circuit board manufacturing industry uses the most suitable automated inspection methods for the production and assembly circuit, depending on the complexity. the required inspection speed and production volume. As a general rule, increasing circuit board complexity, volume, and speed require higher inspection costs.