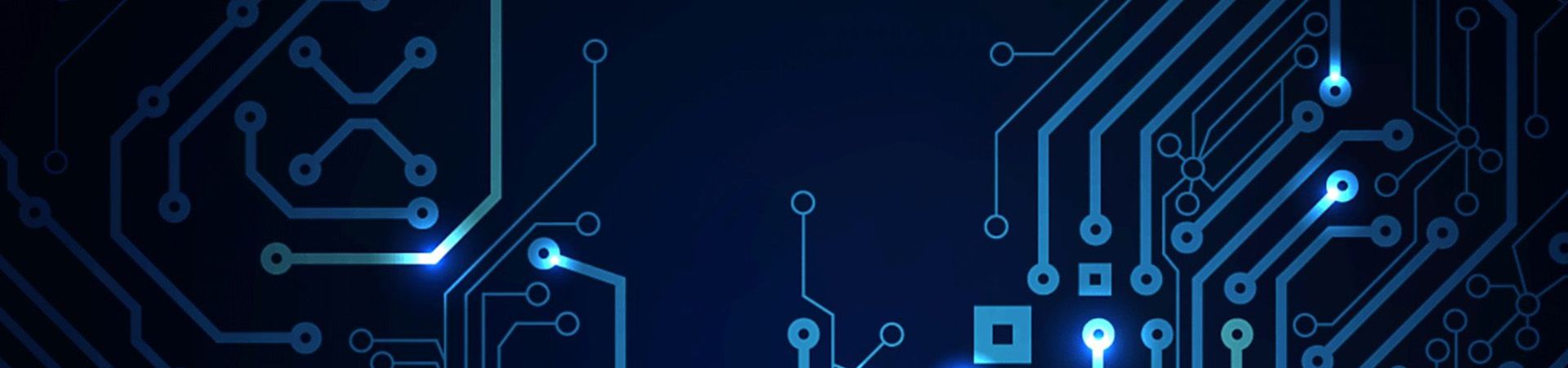
In the realm of printed circuit boards (PCBs), surface finishing techniques are critical to ensuring the integrity and reliability of electronic components. Among the various surface finishing options, gold plating and immersion gold stand out as two popular choices. Both methods offer unique advantages, but understanding the differences between them is vital for making informed decisions in PCB fabrication design and manufacturing.
This blog post will deep dive into the differences between gold plating and immersion gold processes, exploring their applications and implications.
Gold Plating: Enhancing Durability and Conductivity
Gold plating, a traditional and popular surface finishing technique, involves depositing a thin layer of gold onto the exposed copper traces of a PCB. The process typically utilizes an electroplating method, wherein an electrical current is applied to the printed circuit board submerged in a gold-containing solution. The gold ions are attracted to the copper surface, creating a uniform gold layer.
Advantages of Gold Plating:
Enhanced Conductivity and Low Contact Resistance Gold's exceptionally high electrical conductivity underpins its deployment in applications demanding low contact resistance and uninterrupted signal propagation
Excellent Solderability: The gold-plated surface serves as an ideal medium for solder joint formation, fostering reliable and consistent solder connections critical to operational efficiency.
Corrosion and Oxidation Resistance: Gold's innate immunity to corrosion and oxidation ensures PCB longevity, making it a preferred choice for mission-critical electronics operating in challenging environments.
Gold Wire Bonding Facilitation: Gold plating's compatibility with wire bonding techniques strengthens its suitability for advanced semiconductor packaging, enabling robust interconnection architectures.
Immersion Gold: Immersing for Consistent Coating
Immersion gold, also known as ENIG (Electroless Nickel Immersion Gold), is an alternative surface finishing method widely used in the electronic PCB industry. Initially, a conformal layer of electroless nickel is deposited, serving as a diffusion barrier and a foundation for subsequent gold deposition. The immersion gold layer is then chemically applied onto the nickel substrate.
Advantages of Immersion Gold:
Flat and Uniform Coating: Immersion gold provides a flat and consistent gold layer, making it ideal for fine-pitch surface mount technology (SMT) components.
Precise Gold Layer Control: Immersion gold delivers superior control over gold layer thickness, enhancing reliability by minimizing variations and ensuring conformity to design specifications.
Suitable for SMT Assembly: One of the major advantages of immersion gold is that the even surface of this type of PCB assembly helps to evenly distribute solder paste during assembly. It helps in high-quality soldering, which is essential for PCB assembly.
Reflow Stability: Immersion gold exhibits excellent stability during reflow processes, reducing the risk of surface defects.
Key Differences Between Gold Plating and Immersion Gold:
Thickness:
One significant difference between gold plating and immersion gold lies in the thickness of the gold layer. Gold plating typically results in a thicker coating, ranging from 3 to 50 microinches (µin) or more, depending on the application and specification. On the other hand, immersion gold coatings are relatively thinner, usually ranging from 3 to 5 µin.
Deposition Method:
The deposition processes for gold plating and immersion gold are fundamentally different, impacting the distribution and adhesion of the gold layer on the PCB surface. Gold plating is an electrochemical process that involves the use of an electric current to deposit gold ions onto the exposed copper surface. This results in a highly adherent gold layer that conforms closely to the underlying copper features. The electroplating process allows for precise control over the gold thickness, making it suitable for applications requiring specific gold layer thicknesses.
Immersion Gold:
In contrast, immersion gold is achieved through a chemical process involving the deposition of gold on the copper surface without the application of an external electric current. The immersion process relies on a chemical reaction to selectively deposit the gold, resulting in a more uniform and planar gold layer compared to gold plating. This process is particularly advantageous for PCBs with fine-pitch components and complex surface topographies, as it ensures consistent coverage over intricate features.
Solder Joint Integrity and Whisker Formation:
Gold plating and immersion gold shares distinct attributes concerning solder joint integrity and whisker formation. Gold plating's thicker layer provides robust solder joints, offering increased reliability in harsh environments and applications subject to frequent thermal cycling.
In contrast, immersion gold's thinner layer might lead to slightly weaker solder joints. However, immersion gold is less prone to whisker formation - the growth of thin metallic filaments over time. Whisker formation can cause electrical shorts in high-density PCBs, making immersion gold a preferred choice for critical applications requiring long-term stability.
Conclusion:
In summary, the choice between gold plating and immersion gold in PCB surface finishing depends on the specific requirements of the application. Gold plating excels in enhanced conductivity and corrosion resistance, while immersion gold offers a flat and uniform coating, ideal for fine-pitch SMT components. Both methods have their unique advantages, and understanding their differences empowers PCB designers and manufacturers to select the most appropriate surface finishing technique for optimal performance and reliability.