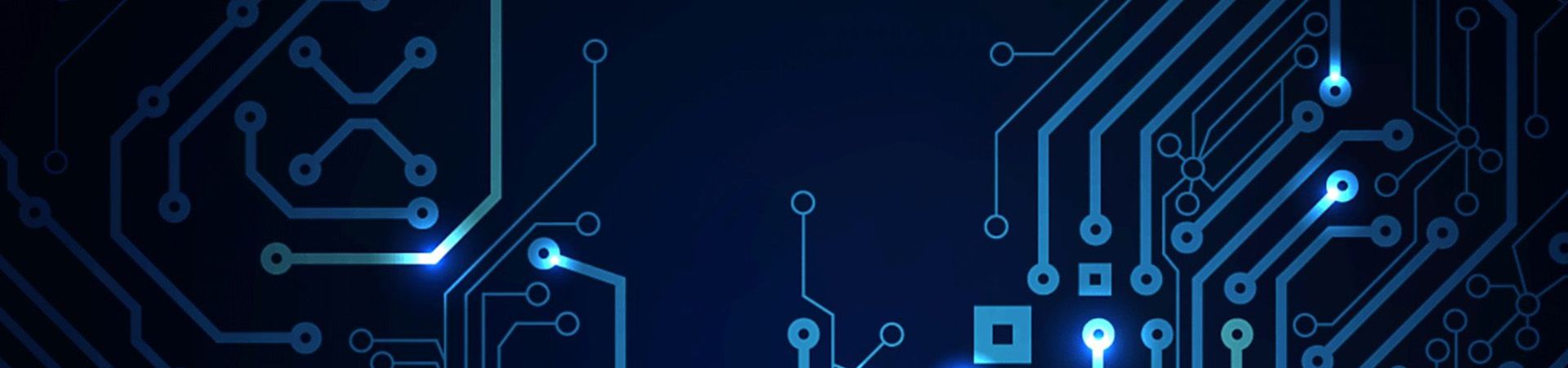
Important Considerations for PCB Circuit Design of a Multi-Layered Board — Part II
PCB circuit design, printed circuit boards, electronic circuit board
Part I of this series dealt with generating the schematic diagram, net list, and the Bill of Materials during the PCB circuit design. Part II will discuss the considerations designers must have when:
- Laying out the components for a multi-layered printed circuit board
- Routing the traces most effectively
Boundary Layout of the Printed Circuit Board
Prior to starting with the component layout, it is necessary for the designer to know the outer boundary of the printed circuit board, its internal cutouts, mounting points, and the position of restricted areas for connectors and other mechanical parts. Usually, this information is available in the form of either a paper drawing or a mechanical CAD drawing.
The designer must import this boundary layout information into their PCB CAD software. They can then proceed to use the net list generated earlier to download the footprints of all the components in the schematic. Initially, all the footprints will be available in the form of a jumble. The PCB CAD software can rearrange the footprints such that the distribution of components is uniform within the boundary.
Components Layout
The way the software rearranges the components inside the printed circuit board boundary may not be acceptable to the designer. The designer must redistribute them according to circuit blocks:
- Actually present in the board (if there are more than one PCBs)
- Operating at different frequencies
- Handling digital and analog signals
- Handling low and high power
- Connected to different voltages and grounds
For instance, as the mechanical layout has already fixed the position of a connector, the designer will find it easier if they place components associated with the connector close to it. The interconnecting traces will be shorter and take up minimum space on the board.
Special Considerations for Components Layout
There are several considerations the designer must be careful about when laying out the components during a PCB circuit design. They mostly relate to:
- Mechanical Considerations
- Electrical Considerations
- Functional Considerations
Mechanical Considerations
Manufacturers prefer making PCBs in panels. Each panel has several individual PCBs that they separate after the fabrication is complete. The separation process causes some mechanical stress to individual boards. If there are components placed near the separation lines, the stress will transfer to these components, damaging them. The designer must be careful to place components some distance away from any separation line. Designers must allow similar spacing of components from mounting holes and other openings in the printed circuit board.
Assembling electronic circuit boards requires the use of automated placement machines for placing components. However, these machines are unable to insert some bigger components or components that use holders (like batteries). These components require manual placement. The designer must be careful to allow for finger spacing around such components for easy placement.
While reflow soldering, larger components can absorb more heat, starving smaller components around them from being uniformly heated. This unequal heating affects the quality of soldering on the board. The designer must be careful to leave adequate space around large components and place smaller components only after this area.
Some connectors may have latches on their ends to hold the counterpart securely. The designer must allow adequate space for the latch to flex and not place any component in the flexing path.
Electrical Considerations
The designer must be careful to not mix low voltage circuitry and high voltage circuitry. They must respect creepage and clearance margins. If they cannot maintain proper creepage distance, they may create a slot in the PCB to increase it.
In a similar way, designers must not mix circuits operating at low frequencies with those operating at higher frequencies. At higher frequencies, circuits may generate electro-magnetic interference or EMI, which circuits operating at lower frequencies may be susceptible to. This may cause the electronic circuit board to fail EMI/EMC tests later.
Grounding is another important consideration for designers. They must separate circuits for:
- Low power grounding
- High power grounding
- Analog grounding
- Digital grounding
- High-Frequency grounding
Although all these grounds meet at the power supply ground, designers may have to consider daisy-chaining them or star-connecting them to achieve the lowest interference and noise during operation.
Functional Considerations
LEDs mounted on the board may have light guides to direct their light to the front panel. The designer must leave adequate space near the LEDs to place the light guide. Likewise, on-board fuses may need replacement and designers must allow for such repairs.
Typically, it is customary for designers to place all components either along the X-axis or along the Y-axis, with all cathodes and positive terminals pointing either up or to the right. Such positioning makes it easier when programming the pick and place machine for auto placement and also for a person who is troubleshooting the board.
Special Considerations while Routing the Traces
There are several considerations the designer must be alert to when routing traces. Most important among them are:
- Setting up Design Rule Check or DRC
- Deciding the number of layers
- Preserving signal integrity
- Avoiding cross talk
- Avoiding sharp bends
- Deciding track width
- Avoiding via-in-pad
- Thermal Considerations
Setting up DRC
Once the designer has finished positioning the components, they may use the auto routing mode of the PCB CAD software to interconnect them following the net list. While routing, the software follows the DRC or Design Rules Check that the designer has set up earlier. The results of auto routing may or may not be satisfactory to the designer. They have the option to manually route some of the traces. They can lock the specific traces they do not want the software to edit, and run the auto router for the rest.
DRC specifies many constraints in the design like minimum spacing between pads and traces, the minimum inner diameter of an annular ring around a via, and many more. If the software is unable to route a trace without violating a DRC rule, it will flag a caution and show the unrouted net.
Deciding the Number of Layers
Routing the traces is a very important stage, as it helps to decide the number of layers a multi-layered board needs. For instance, if it is not possible to route several nets, the designer may have to increase the number of layers. The designer also has the option to reduce the number of layers to optimize the layout and reduce the cost of the PCB.
Preserving Signal Integrity
For high-speed traces, the designer may have to position the trace such that it meets a specific Impedance. For this, they may have to enclose the trace between ground planes and maintain a specific spacing between two traces.
Avoiding Cross-Talk
As adjacent layers are very close together, the designer must take care to not run traces in parallel to avoid cross-talk. Running traces at right angles on adjacent layers usually takes care of avoiding cross-talk.
Avoiding Sharp Bends
It is difficult to etch traces with sharp bends. Moreover, sharp corners may retain the etchant, leading to corrosion of the trace later. Designers must avoid sharp bends wherever possible when laying out the traces.
Deciding track width
Power carrying traces must have adequate cross-sectional area to present a low resistance. As the thickness of copper is a constant throughout the layer, the only variable available to the designer is the track width. The designer must calculate the width required before setting up the trace. Air convection can remove heat from traces on the two outermost layers, but traces on inner layers must dissipate their heat only through the surrounding dielectric material. Therefore, designers must add more width to traces on inner layers.
Avoiding Via-in-Pad
It is tempting to save space by placing a via within a pad. However, during reflow soldering the via acts like a capillary and wicks the molten solder away from the pad. This leaves the pin and pad without a bond of solder, causing electrical disconnection.
The designer must not place vias within a pad, unless they plan to have the via filled and or tented. They must place all vias at a small distance from the pad, with a dam of solder resist separating the two.
Thermal Considerations
It is customary to have certain components generate heat during operation. To remove the heat, the designer may have to place a number of thermal vias under the component. Thermal vias usually connect to a copper surface on the outer layer where a heat sink can remove the heat.
Conclusion
There are several considerations for the designer during the PCB circuit design of a multi-layered electronic circuit board.Most considerations are mutually dependent, which means a change in one affects another, and the designer must balance the two for optimum results. Finally, the entire printed circuit board design must undergo a Design for Manufacturing or DFM and a Design for Assembly or DFA review to remove any issues that may crop up during manufacturing and assembly.