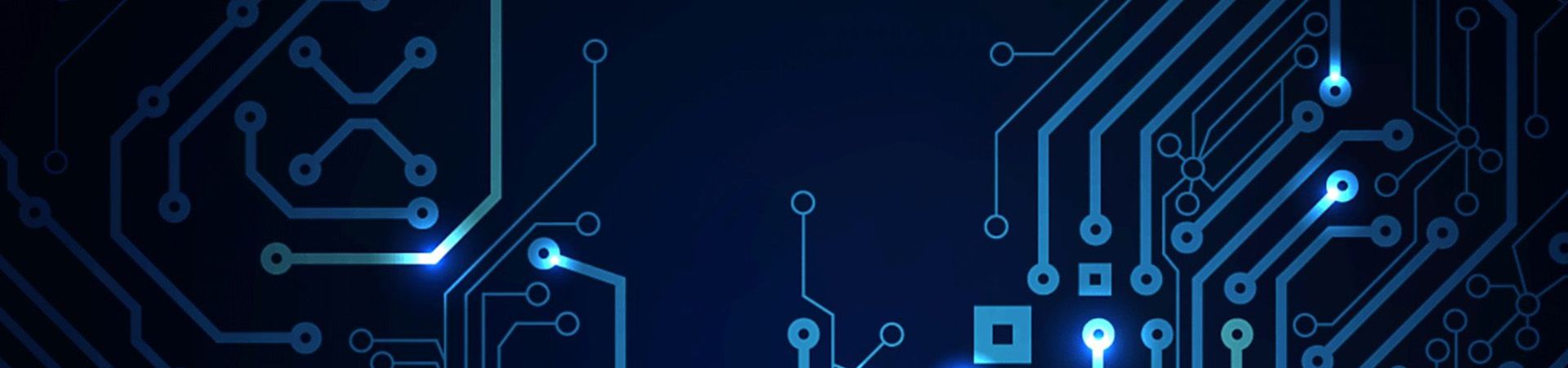
The Role of PCBs in Electric Vehicle Design: Challenges and Innovations
The transportation industry is observing a rapid change. To combat pollution, find alternate fuel options, and make travel more efficient and comfortable, electric vehicles have emerged as a solid product. However, have you ever given any thought to what makes EVs so sophisticated and reliable? Print circuit boards (PCRs) are the backbone behind these breakthrough technologies. Your EV ideas are powered and controlled greatly by these small but mighty components.
In this blog, we will explore how PCBs are aiding the development of electric vehicles and their indispensable nature in your EV manufacturing process.
Role of PCBs in Electric Vehicles
In simple words, EVs are controlled by printed circuit boards. As technology is taking the front seat of modern transport systems, the importance and applications of PCBs are increasing. Here are some EV component systems where PCBs are essential.
- Battery Management Systems (BMS): The core of an electric vehicle is its battery. Hence, efficient management of it is absolutely important. By spotting problems like overheating or short circuits, PCBs in a BMS monitor and control charging-discharging cycles, balance power distribution across battery cells, and maintain safety.
- Motor control: The management of the electric motor of the EV depends mostly on PCBs. They vary the motor's torque and speed. PCBs are also made to maximize energy use for the best performance. Modern PCBs are also made to manage high-current loads easily.
- Power Inverters and Converters: Power inverters transform battery DC voltage to AC for the motor by means of metal-core PCBs. Analogous energy flow between high-voltage and low-voltage systems is managed by PCBs in converters, therefore guaranteeing smooth functioning.
- Power distribution: PCBs help distribute power from the battery to the motor, lights, infotainment systems, and more. Effective power distribution allows your EVs to stay reliable and deliver peak performance.
- Communication Systems: The performance of an EV depends heavily on the harmonic operations of several systems. PCBs help to guarantee accurate and fast transmission of data from sensors and controllers, therefore facilitating this communication.
How Will Electric Vehicles Impact the PCB Industry?
With the increasing concern about environmental pollution and scarcity of fossil fuels, vehicle manufacturers are rapidly moving towards electric vehicles. According to reports, the EV market will grow at a CAGR of 6.63% from 2024 to 2029(1). This growth directly indicates the rising demand for reliable PCBs. By 2029, the worldwide PCB market is expected to reach at least $92.39 billion (2). This demand will keep PCB manufacturers under pressure to compete with one another, perhaps generating major technological improvements in doing so. EVs need PCBs that can be compact, handle clean energy conversion, and support the IoT.
Challenges in EV PCB Design
While PCBs unlock incredible possibilities in EVs, they also present unique challenges due to the demanding environment and high performance required:
- High Power Density: EVs require PCBs capable of handling high power loads without compromising safety. This increases the need for specialized materials and advanced designs.
- Thermal Management: As EV systems generate significant heat, ensuring effective heat dissipation is a critical challenge for PCB designers. Materials like insulated metal substrates (IMS) and thermal vias are often used.
- Size and Weight Constraints: Automakers demand compact and lightweight designs to optimize vehicle efficiency, posing design limitations for PCB engineers.
- Reliability: PCBs in EVs must endure extreme temperatures, vibrations, and prolonged use without failure. Achieving this reliability requires stringent manufacturing standards and rigorous testing.
Innovations Driving the Future of EV PCBs
Linked systems, automated driving, and electric cars (EVs) are transforming the automotive industry. Circuit boards have to get smaller, stronger, and smarter if we are to enable breakthrough automobile technology.
- Stronger:
Increasing dependability and durability: Extreme temperatures, vibrations, and chemical and moisture exposure provide difficulties in automotive settings. Circuit boards of the future have to be strong enough to withstand these circumstances. Modern materials guarantee constant performance and increase longevity by means of high-temperature laminates and conformal coatings.
- Smarter:
Supporting Innovative Technologies: The development of intelligent cars calls for more intelligent circuit boards that are able to handle challenging tasks. High-frequency PCBs are being developed to allow high-speed computation and connectivity from real-time data processing for autonomous systems to seamlessly interface with IoT networks.
- Smaller:
Space-saving miniature designs: Modern cars have ADAS, infotainment, and battery management systems. Compact circuit boards are required for limited space. Multilayer PCBs and HDI allow engineers to fit more functionality into fewer spaces.
Why Choose PCB Power for EV PCBs?
At PCB Power, we understand the complexities and requirements of PCBs for electric vehicles. With advanced PCB manufacturing capabilities and expertise in prototype and production services, we offer:
- Tailored Solutions: Multilayer PCBs, HDI boards, and materials suited for high thermal and power demands.
- Reliable Manufacturing: High standards of quality control, certifications like IPC Class 3, and advanced manufacturing technologies.
- End-to-End Support: From layout assistance to fast prototyping and volume production, we ensure seamless service to meet your project needs.
Key Takeaways:
Whether you drive a fossil-fuel-powered car or run an EV, PCBs are everywhere around you. If you are looking for a custom PCB solution, you require a manufacturer who can guide you through all phases of the process and has industry knowledge.
Click here to get a free quote instantly for your EV projects.