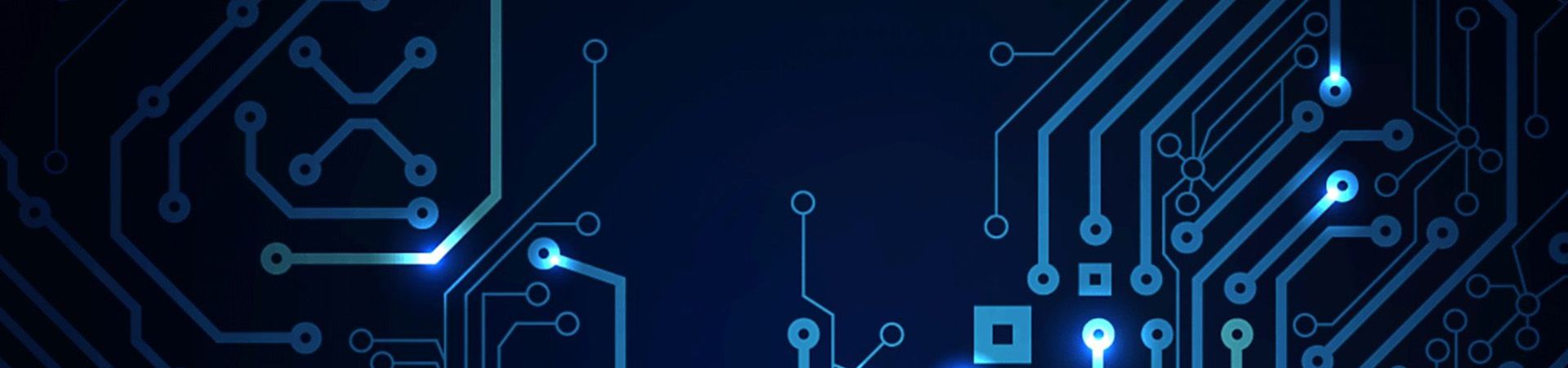
SMT vs SMD vs Through Hole vs BGA - Choosing the Best Method for PCB Assembly
Monday, 08 July 2024
PCB Power
SMT vs SMD vs Through Hole vs BGA - Choosing the Best Method for PCB Assembly
High-performing PCB assembly in India is mostly dependent on selecting the optimal component mounting techniques. It affects everything, including the size and functionality of your PCB, as well as its overall price. To help you select the best option, let's examine Surface Mount Technology (SMT), Surface Mount Device (SMD), Through Hole Technology (THT), and Ball Grid Array (BGA).
Surface Mount Technology (SMT)
In Surface Mount Technology (SMT), components or surface mount devices (SMD) are assembled on a PCB's surface.
Surface Mount Devices (SMD)
The term "surface mount device" (SMD) describes an electrical component that fits neatly on the surface of a PCB. Here, the soldering paste and process are used to fix the SMDs to the printed circuit board surface.
Features of SMD
- Size and Weight: The compact size and light weight of SMDs make them ideal for use in modern, tiny electronic products.
- Performance: Their shorter lead lengths translate into better electrical performance at high frequencies.
- Cost-effectiveness: Automated placement and soldering make SMDs a more cost-effective choice for large production.
Ball Grid Array (BGA):
These are particular types of SMT components in which a grid of solder balls on the underside of the component creates the electrical connection with the PCB.
Advantages of BGA
- High pin count: A pin count powerhouse, BGAs are ideal for high-performance devices like microprocessors because they pack a ton of connections into a little package.
- Electrical efficiency: Ball grid arrays (BGAs), with their shorter solder ball connections, can outperform traditional leaded components electrically.
You can read more about advantages and applications of Ball Grid Array (BGA) here.
Drawbacks of BGA:
- Tough to inspect: Examining BGA solder joints is challenging because they are beneath the component. The use of an X-ray examiner is often required.
- Rework Ramifications: Because BGA connections use fragile solder balls, reworking them is an expensive and difficult process.
Surface Mount Technology (SMT) is like a high-tech way of putting together electronics. Instead of sticking parts through holes in a board, SMT places them right on the surface, which helps make gadgets smaller and more efficient. The parts used in this process are called Surface Mount Devices (SMD). These tiny components, like little resistors and capacitors, are what allow us to have slim smartphones and powerful laptops.
Benefits of SMT:
- Accuracy and speed: In this SMT process, the pick-and-place machines handle surface mount devices (SMD) during the PCB assembly process. It greatly improves the speed and accuracy, reducing assembly time and cost.
- Space utilization: Using SMT, the SMD or components can be assembled on both sides of the PCB. It allows you to use twice as much area for complex designs as you do with Through Hole Technology.
- Performance: Smaller sizes and shorter leads of SMT components provide better, higher-frequency electrical performance.
Drawbacks of SMT:
- Strict inspection: Because surface mount technology components are so small, only strict inspection techniques can guarantee exact placement and soldering.
- High rework: Due to small and complex components, reworking surface mount technology might be difficult.
- Heat sensitivity: Some SMT components can be permanently damaged by soldering.
Through Hole Technology (THT)
This is part of the process when the PCB is prepared by drilling holes and then soldering components with leads into those holes.
Benefits of THT:
- High reliability: The higher mechanical strength of THT components makes them ideal for applications involving significant stress or vibration.
- Easy inspection: During an inspection, it is easier to visually verify larger THT components for proper placement and soldering.
- Easy rework: Larger size and easy access to THT solder junctions make them usually easier to work with when it comes to rework.
Drawbacks with THT:
- Comparatively bigger in size: As THT is larger in size compared to surface mount technology components, it is harder to accommodate as many components on a board and may even cause the board to be larger overall.
- Less efficiency: Because THT assembly needs more manual work, it is less efficient for mass manufacturing than SMT.
The Careful Balance while Selecting the Best Method
Which technology works best for your project depends on its particular needs. Consider the following key points:
- Board Size and Density: Surface mount technology is the better option for applications with less space.
- Production Volume: Because of its automation benefits, SMT provides significant cost savings in terms of production volume.
- Component Strength: Mechanically demanding components are best constructed using THT for strength.
- Performance Objectives: If the funds and experience are available, BGAs may be the best option for high-performance applications that need a lot of pins and exceptional electrical characteristics.
- Criteria for inspection and rework: Here Are Some Advantages of THT. SMT inspection techniques are always changing.
- Budgetary considerations: The automation benefit of SMT allows for substantial cost reduction in assembly, which affects the budget. It helps, especially in large-scale production. Still, remember that SMT could cost more for rework.
In the dynamic field of electronics manufacturing, mixed PCB assembly is a technique that blends surface-mount and through-hole components. You can read more about Benefits of Mixed PCB Assembly here
Key Takeaways:
With most printed circuit boards designing and manufacturing processes, one approach cannot bring the desired results. Combining these technologies can improve your outcomes to the maximum. The best result for your particular project depends on your knowledge of the advantages and disadvantages of each technology.
Being a major participant in PCB assembly in India, PCB Power uses the best technology available to guarantee optimal performance depending on the needs. Click here to get a quote or make an online purchase. Contact us at [email protected] or tel:+91 7600012414 if you have any more questions about our PCB service.