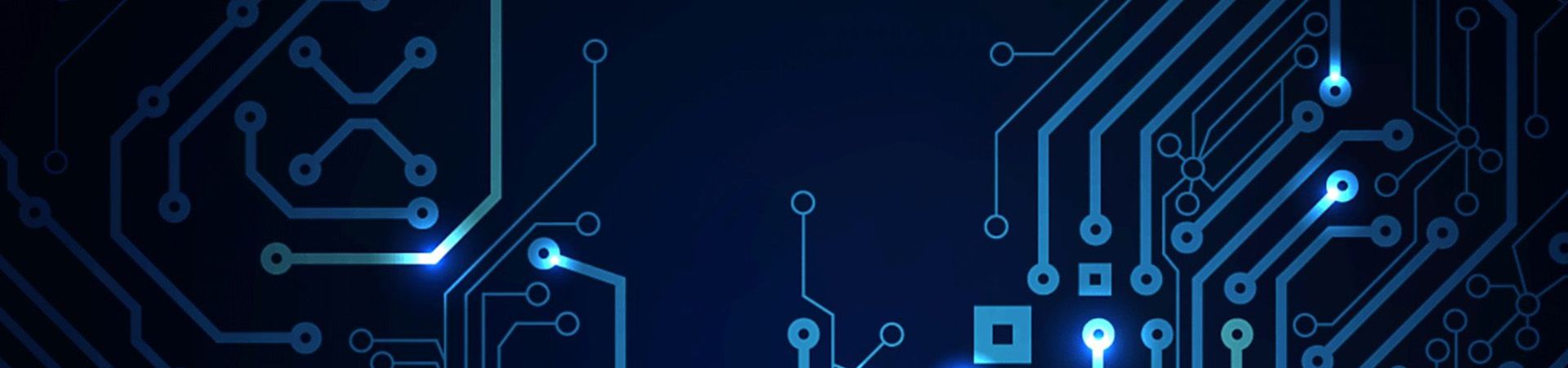
The Importance of Countersink Holes in PCB Fabrication
Electronic devices rely on printed circuit boards (PCBs) to link their components in complex ways. Every small detail plays a crucial role in making the product reliable and efficient. A reliable and high-performance printed circuit board depends on high precision in every aspect, from the components used to the drilling technique. One absolutely important design parameter is countersink holes.
This article will highlight why countersink holes are essential for PCB performance, applications and aesthetics. Read on to learn more.
Countersink Holes: A Brief
The countersink hole is a little conical hole drilled into your PCB board and other essential parts like fabrication. Using countersink screws results in either a slightly below surface or a flush with the board surface. This becomes crucial when you require a PCB to fit tightly inside an enclosure free of any screws protruding. It ensures no interference with the design of other components or compromising the general performance of your completed product.
Imagine you’re assembling a piece of furniture, and you want the screws to sit flush with the wood surface. A standard hole won’t do the trick, but a countersunk hole ensures the screw fits in neatly. The same logic applies to PCBs, where flush-fitting screws contribute to a smooth, efficient design.
Why are Countersink Holes Important?
Countersink holes go well beyond a design decision. They will greatly affect the lifetime and performance of your PCB:
1. Better Stability and Durability
Countersink holes help fasteners fit securely and flush with the PCB surface, which is important for the overall mechanical stability of the board. This is especially crucial for PCBs used in devices that experience vibrations or movements, like smartphones, automotive electronics, or industrial machinery. Without countersunk screws, the fasteners could shake loose, damaging components or causing misalignment over time.
2. Sleek and Professional Design
In products where the appearance of the PCB is visible or matters to the final product’s aesthetics (think open-frame gadgets or wearables), a clean and flush finish is key. Countersink holes allow screws to sit below the surface, giving the board a polished, professional look. It’s not just about how well the PCB works, but also how it looks.
3. Maximizing Space in Tight Designs
Modern electronics often require very high-density PCB designs, where every bit of space is valuable. Countersinking fasteners allows you to maximize the surface area on your PCB. Since the fasteners don’t protrude, designers have more freedom to place additional components or routing on the surface, which is critical for complex and compact boards.
4. Electrical and Thermal Efficiency
Countersink holes may also offer some extra functionality beyond mechanical stability. In certain applications, flathead screws seated in countersink holes can act as grounding points or help dissipate heat. This can improve both the electrical performance and heat management of high-power PCBs.
Types of Countersink Holes
There are two common types of countersink holes used in PCB designs:
1. Simple Countersink Hole
This is the most basic type, where a conical hole is drilled to match the angle of a flathead screw. The screw head sits flush with the PCB surface, making it perfect for applications where both a clean finish and structural stability are needed.
2. Counterbore Hole
Unlike a countersink hole, a counterbore hole is cylindrical and allows the screw head to sit even deeper into the PCB. This type is useful when you need even more clearance above the fastener. Counterbore holes are typically used for larger screws and applications requiring more mechanical strength.
Where are Countersink Holes Used?
Countersink holes find their way into various industries, each with its own requirements. Here are a few examples:
1. Consumer Electronics
In smartphones, tablets, and other portable devices, countersink holes ensure screws are neatly tucked away. This helps maintain the sleek design that consumers expect while also preventing any interference with the functionality of the device.
2. Automotive Electronics
In the automotive industry, electronic components are often subject to constant vibrations and high-stress environments. Countersink holes ensure that fasteners remain securely in place, protecting the PCB from wear and tear.
3. Industrial Machinery
Heavy-duty machines need durable PCBs, and countersink holes contribute to this durability by providing strong, flush connections for fasteners. This helps the machinery operate smoothly, even in harsh conditions.
4. Aerospace and Defence
When it comes to aerospace and military applications, space and weight are always at a premium. Countersink holes enable compact designs without compromising the strength or reliability of the PCB, making them a go-to feature in these industries.
Design Considerations:
Designing for countersink holes calls for some consideration in several aspects:
- Choice of screws: The kind of screw you intend to use will define the suitable countersink depth and angle. Basically, there are two types of countersink holes that are preferred- V type countersink holes and T type countersink holes.
- PCB thickness: The thickness of your PCBs will affect the depth of the countersink hole also known as counterbore depth.
- Component clearance: Ensure the countersink hole's surrounds allow enough room to prevent conflicts with surrounding components.
- Manufacturing tolerance: To guarantee a satisfactory fit, give thought to the PCB and the screw tolerance assembly.
- Chamfer angle: The hole wall and board surface angle is usually 90-100°. Larger angles over 100° increase head clearance but decrease edge support and laminate strength near the hole. Below 90° angles are possible but harder to make.
Key Takeaways:
Manufacturers can produce high-quality electronic products that meet stringent performance standards by effectively incorporating countersink holes into PCB designs and considering practical design considerations. Including countersink holes into your PCB design produces a product that looks great, runs perfectly, and extends its lifetime. As you keep improving your PCB manufacturing techniques, never ignore this apparently minor but vital characteristic.
Count on PCB Power to be your trusted partner in providing top-notch, dependable PCBs for all your essential applications. For a comprehensive understanding of technical capabilities of PCB Power, we invite you to explore our resource page.
Contact us if you want further information about our products, manufacturing techniques, and ways they would help your projects. You can reach us via email at [email protected] or call us at +91 7600012414. Let's team up to empower your ideas!