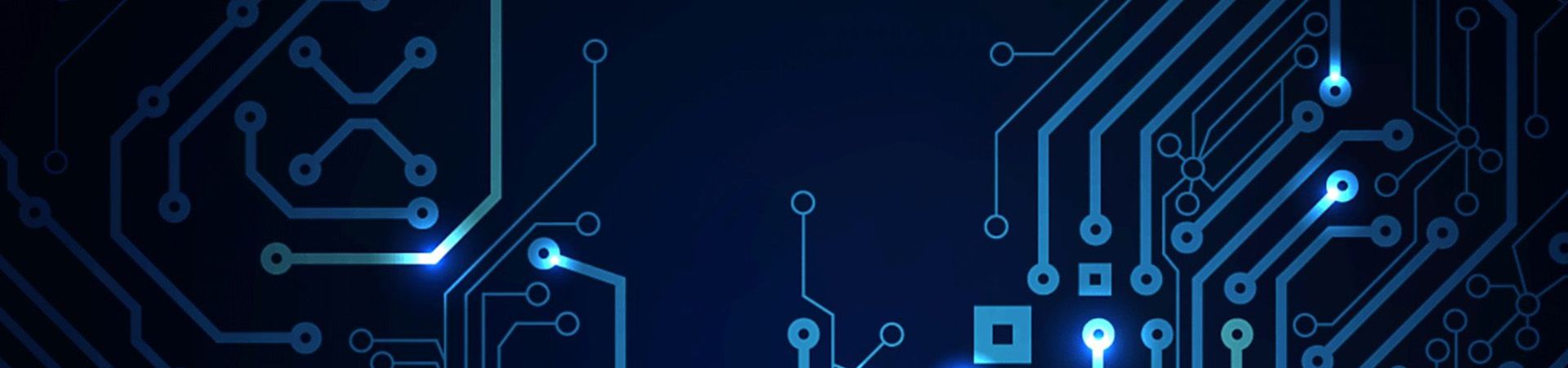
What are Peel Off, Countersunk & Impedance Control in Printed Circuit Boards?
Circuit board fabrication requires meeting several PCB circuit design functionalities. The PCB production industry assigns special names to identify them. Among various types of functionalities in use, some are easy to understand, while others may be confusing. We will explain three such functionalities that are very important for a proper and effective operation of the printed circuit boards:
- Peel Off—Mask and Damage
- Countersunk—Holes
- Impedance Control—High-Speed Boards
Peel Off
In the context of printed circuit boards, there may be two types of peel-offs:
- Peel-Off Masks
- Peel-Off Damages
Peel-Off Masks
PCB circuit design may often require a peel-off mask to cover a certain area of the PCB to prevent a specific state of processing from affecting the covered area. For instance, a printed circuit board may have a temperature-sensitive component that cannot withstand exposure to high soldering temperatures usual in ovens, and operators must solder them manually. Fabricators cover the pads of the component with a peel-off mask to prevent solder from covering the pads during the wave soldering process and allowing manual soldering of the component later.
PCB production may require making boards with multi-surface finishes like bondable gold, hard gold, or carbon ink along with ENIG or Immersion silver. As fabricators cannot apply them together, the first surface finish requires protection from the application of the balance of the surface finishing. Peel-off masks, also known as peelable masks are a reliable, time-saving, and inexpensive process rather than using Kapton and other heat-resistant tapes.
Some areas of the PCB do not require any processing during assembly. A peel-off mask ensures sensitive features in such areas remain protected from splash damage during various processing stages.
The assembler can remove the peel-off mask after other processes to allow special processing of the protected area. It is easy to remove a peel-off mask by lifting one edge and pulling away slowly from the PCB surface. Peel-off masks usually do not leave any residue or particles on the printed circuit board surface, and therefore, require no additional cleaning.
Generic PCB Circuit Design Rules for Peel-Off masks
- Restrict application of peel-off masks to only one side of the board, preferably the bottom side
- For peel-off masks on both sides of the board, clear instructions are necessary along with a layer sequence description in the mechanical layer of the drawings.
- The output file for the peel-off layer must include the board outline.
- Preferably use one large area for a peel-off mask rather than several small areas randomly placed. Alternately, connect separate peel-off areas together as far as possible. This helps in easier removal of the peel-off after the soldering process is over.
Properties of Peel-Off Masks
Most peel-off masks in the PCB industry are non-staining, non-contaminating, and non-corrosive. This is essential to the success of an electronic circuit board assembly process.
Peel-off masks are typically RoHS compliant, and applicable to all surface finishes. They are stable up to 288 °C (550 °F), are environmentally safe with low toxicity, and are phthalate-free.
Peel-Off Damages
A printed circuit board constitutes many layers. The outermost layers have a potential capacity to peel off, causing damage to the board. The most common peel-off damage occurs with the solder mask and the copper layer. The solder mask or the copper pad or track lifts off from the PCB surface, causing peel-off damage.
Although there are several reasons for peel-off damage to happen, the major cause is heat. The solder mask and copper layer bond to the surface of the substrate during PCB fabrication. While the copper layer requires heat and pressure for the adhesive to bond, the solder mask requires heat to cure it and bond. Inadequate heat and pressure can cause premature bonding, leading to a peel-off when the board is subject to additional heat during the soldering process. Solder mask peel-off can happen when the PCB is undergoing tinning in an automatic tin furnace.
Another reason for copper peel-off is the application of intense heat, especially during manual rework or manual soldering. The high heat from the soldering iron or gun damages the bond between the copper layer and substrate, causing a lift-off of the copper layer.
To prevent peel-off damage to the solder mask, it is necessary to allow it adequate time for a full cure. To prevent peel-off damage to a copper layer, it is necessary to allow only the use of temperature-controlled soldering irons set below the maximum temperature recommended by the PCB manufacturer.
Countersunk Holes in Printed Circuit Boards
Many fixtures on an electronic circuit board require screw-fixing to hold them firmly in place. If the screw head protrudes beyond the board surface, the overall thickness may become greater than permissible. Two ways to avoid the situation are by drilling:
- Counterbore Holes or
- Countersunk Holes
Both drilling methods offer a screw fitting that sits flush with the surface and offers a clean look to the installation. However, each method has its own merits and demerits.
Counterbore Holes
These are stepped holes with a smaller diameter for the screw shank stepping to a bigger hole to accommodate the screw head. The requirement for the screw to sit flush with the surface is that the thickness of the screw head must be less than the board thickness. This requirement makes it difficult to use counterbore holes on thin printed circuit boards. Moreover, the sharp transition from a bigger diameter to a smaller diameter makes the PCB weaker.
Countersunk Holes
Rather than a stepped hole, it is more common to use a conical or tapered hole in the PCB to accommodate a flat head socket cap countersink screw. For proper PCB production, the designer must provide the fabricator with specific details like:
- The side of the board the countersink must be on—top or bottom.
- The countersink diameter.
- The angle of the countersink or its taper angle.
- Depth of the countersink.
- Finished diameter of the shaft hole.
- Whether the hole shaft and sink need through plating.
Impedance Control
When printed circuit boards operate with high-speed signals, the impedance they offer has significant implications on the quality and integrity of the signals. For proper functioning, the impedance of the signal path on the PCB must match the impedance of the source and the load.
Designers can exercise control over the impedance of the PCB in two ways:
- Fixing the dielectric thickness of the PCB
- Mentioning the impedance in Ohms
Fixing the dielectric thickness in the PCB is easy, but this may or may not give the desired impedance. Apart from the thickness, the impedance of the signal path also depends on the characteristics of the material of the substrate. Therefore, if the fabricator decides to use a different material for the substrate, they may miss the desired impedance value.
Mentioning the impedance in Ohms is a better practice, as it offers the fabricator a choice in selecting the material and adjust its thickness to meet the impedance value. The board fabricator might have to make some changes in the design or dimensions to ensure they meet the specified impedance. During circuit board manufacturing, it is usual for the impedance to vary with a tolerance of ±10 Ohms.