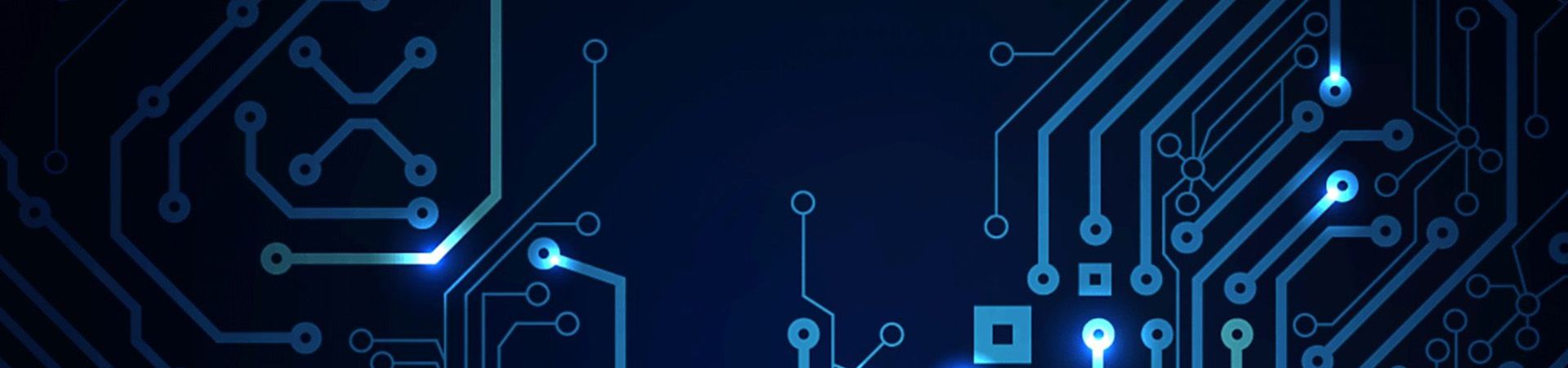
What is Conformal Coating?
Introduction:
The brain of any electronic equipment, starting from your mobile device to the most advanced spacecraft, is the printed circuit board. Interestingly, your electronics will benefit most from the right kind of PCB coating and application techniques. As miniaturized electronics and circuits have become more common, conformal coating application has seen a meteoric rise to confirm its significance in a plethora of modern PCB-related applications.
This blog will provide you with all the knowledge required to select the perfect conformal coating for your application needs. If you are looking for anything in particular, the details in this blog are available for a more targeted approach.
What Makes Conformal Coating Necessary?
Your PCB is exposed to several environmental hazards. Improper protection allows humidity, pollutants, and other elements to cause corrosion, short circuits, and performance loss. Here are the reasons for your thinking on conformal coating:
- Moisture Resistance: Prevents short circuits and oxidation.
- Dust and Chemical Protection: Guarantees PCB reliability by means of pollutant shielding.
- Improved Electrical Insulation against temperature extremes: Lowers leakage currents and improves performance in harsh environments like rapid changes in temperature or extreme heat/cold
- Extended lifespan: Protects your electronic components, therefore lowering maintenance expenses.
- Improved Durability: Perfect for high-stress settings like automotive, aerospace, and industrial uses.
What are The Steps of Conformal Coating
To ensure the best output of the conformal coating, there are certain essential steps you need to follow. Consider them rigorously.
- Surface preparation: The procedure starts with surface preparation, which uses solvents or plasma treatment to remove dust, grease, and impurities. Masking covers regions like connectors and test points; the PCB has to be totally dry.
- Coating application: It comes next, and here, a suitable technique like spraying is selected. Applying several thin layers rather than one large one guarantees uniform coverage and avoids flaws such as air bubbles or uneven thickness.
- Drying and curing: After application, drying and curing harden the coating. Air drying, heat curing, or UV exposure can all help to achieve this. Achieving consistent adhesion and lifetime depends on controlled environments.
- Inspection: After curing, Visual Inspection and Automated Optical Inspection (AOI) for high-volume is done to find flaws such as bubbles or excessive thickness. Following industry standards guarantees dependability.
- Final touch-up: Rework and touch-up call for solvent or abrasion removal of faulty coatings, followed by reapplication in impacted areas if required.
- Testing and packaging: Finally, testing and packing confirm PCB operation. Correct packing guarantees the PCB coating is ready for use by preventing damage.
Challenges and Considerations:
Although PCB coating significantly increases endurance, there are specific challenges you ought to understand:
- Controlling Coating Thickness: It is absolutely vital to use the correct thickness. While too thin might not offer sufficient protection against moisture and pollutants, too thick can hold heat and create thermal stress. Automated application techniques provide consistency; compliance with IPC-CC-830 standards helps preserve dependability.
- Eliminate Air Bubbles and Voids: Bubbles and voids compromise protection, hence letting pollutants access the PCB. You can avoid defects by appropriate surface cleaning, vacuum-assisted application, and regulated curing. Curing with gradual temperature ramping helps to prevent voids brought on by coating expansion or contraction.
- Compatibility of Materials: Make sure the selected coating works with PCB parts. Some coatings could not stick well to particular substrates, hence compromising lifetime. In severe conditions, chemical resistance is absolutely vital. While silicone offers flexibility, rigid coatings like epoxy give protection but could fracture under temperature fluctuations.
- Challenges of Rework and Repairability: Removing epoxy coatings is challenging, which makes restorations expensive and labor-intensive. Removable coatings such as acrylic or urethane make rework simpler. Coating after masking important sections first helps to simplify subsequent repairs. Choosing a coating calls for consideration of rework techniques such as chemical stripping, laser ablation, or abrasion.
- Compliance with Environmental Regulations: Make sure that the coating satisfies environmental rules like RoHS and REACH, which limit dangerous chemicals. Some coatings have volatile organic compounds (VOCs) that call for appropriate application ventilation. Choosing environmentally friendly coatings will help to increase sustainability and worker safety.
- Choosing the Correct Application Technique: Coating quality is influenced by various application techniques: spraying, dipping, brushing, or selective coating. While brushing is appropriate for minor repairs, automated spraying guarantees consistency. Selective coating reduces the need for masking by avoiding covering connections and other sensitive regions.
Addressing these issues will help you to maximise effective maintenance and improve PCB life span and dependability.
Key Takeaways:
Investing in conformal coating guarantees that under any challenging circumstances, your PCBs stay functional and work with the same efficiency. Applying the correct coating can significantly improve the performance and lifespan, whether you produce electronics for industrial machinery, automotive uses, or consumer devices.
Searching for Dependable PCB Coating Solutions?
PCB Power understands how crucial PCB life span can be. Our reliable and advanced PCB manufacturing and assembly services guarantee that your electronic designs are safeguarded and constructed to survive. Opt for a conformal coating option on our instant quote page to improve your PCB stability right now!
Register with us to get an instant quote and visit our resource page to learn more about our technical capabilities.