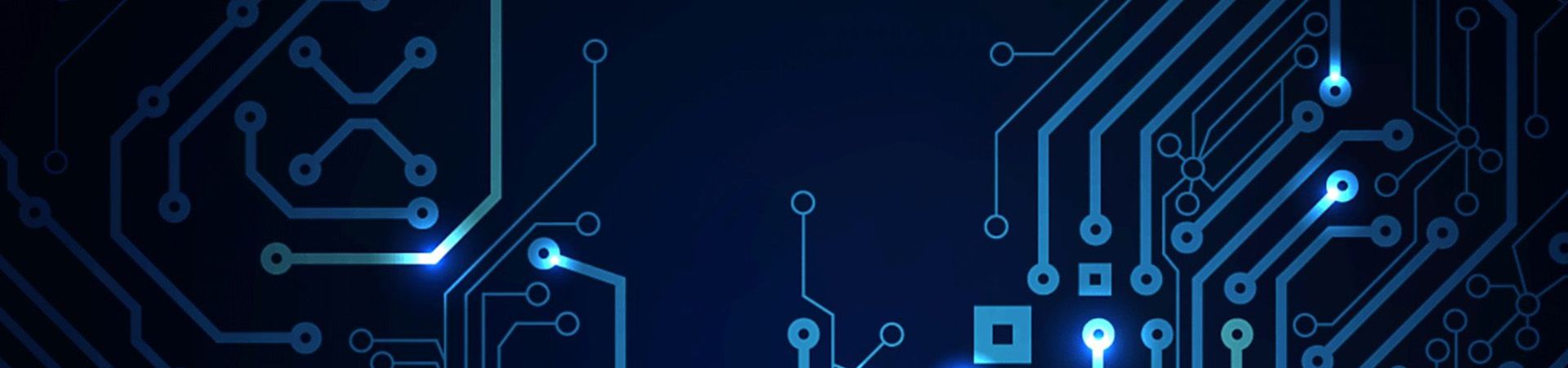
Why Automated Soldering is Better Than Manual for Electronic Circuit Boards
electronic circuit boards, PCB circuit design, printed circuit boards, pcb prototyping services
Solder is the primary material that anchors electronic components to their respective pads on an electronic circuit board. Whether the component is a through-hole component or a surface mount type, the board a rigid one or a flexible type, solder performs two major functions:
- Mechanically anchoring the component to the board
- Providing electrical conductivity between different components
Solder, an alloy of several metals, melts at a low temperature of about 220-260 C, depending on its composition. Manufacturers make electronic components that can withstand this temperature for about 90 seconds. This is the maximum time that operators allow soldering machines to melt the solder and anchor the components. However, there are two processes to achieve soldering:
Manual Soldering
Manual soldering is a local process requiring a soldering iron. This is a metal bit, usually made of copper with a coating of aluminum or steel, heated to about 400 C. Various types of soldering iron are available in the market, from simple ones heated by an electrical wire element to those with sophisticated control systems to regulate their bit temperature.
In application, the operator uses the heated iron bit to heat both the component lead and the pad. Once they are hot enough, the operator holds a solder wire to the junction. The solder melts and flows between the component lead and the pad. On removal of the soldering iron tip, the solder, along with the component and the pad, cools and anchors the component.
Another type of manual soldering uses hot air instead of the hot metal bit. A pump blows a jet of hot air down on the component. This method is suitable mostly for repair, where a single component needs removal and replacement.
Automated Soldering
This method of soldering uses a machine to accomplish the soldering activity. Broadly, there are two types of automatic soldering machines in common use:
- Wave Soldering Machine
- Reflow Soldering Machine
Wave Soldering Machine
This machine is useful for soldering through-hole components and those components placed on the bottom surface of the printed circuit board.. Through-hole components have long leads that must pass through holes in the PCB. Assemblers insert the leads of through-hole components into holes from the top side of the PCB, allowing them to protrude below the bottom side. The PCB circuit design for through-hole components provides pads on the bottom side of the board.
The assembly passes over a bath of molten solder. A pump inside the bath forces the molted solder to flow through a nozzle in the form of a wave. As the board and components assembly passes over this solder wave, the molten solder adheres to the component leads and the copper pads. Once it passes the solder wave, the solder cools and anchors the component to the pads.
Reflow Soldering Machine
The reflow soldering machine is useful for soldering printed circuit boards mounted with surface mount components. These components have very short leads that do not need holes in the PCB to mount them. A pick-and-place machine picks up the tiny surface mount components and places them on individual pads on the PCB. To enable soldering, the operator must place a tiny amount of solder paste on the pads before placing the component on them.
The assembly then enters a reflow soldering machine. Infrared heaters heat the board, the components, and the solder paste between them. At a sufficiently high temperature, the solder paste melts and flows. As the board assembly moves out of the heated zone, the molten solder cools and anchors the components to the pads on the board.
Comparing Automated and Manual Soldering
Most manufacturing processes prefer automated assembly over manual as automation reduces their cost of production while increasing the speed of operations. While manual assembly requires several skilled technicians, a single automated assembly line is enough to do the same job at a faster rate. Moreover, manual assembly always has the chance of human error. The automated machine, once properly set up, will perform consistently and produce high quality output repeatedly.
ACTIVITY | AUTOMATED SOLDERING | MANUAL SOLDERING |
---|---|---|
Throughput | High | Low |
Consistency | High | Low |
Quality | High | Varies |
Resources | One Machine | Several Skilled Technicians |
Process Control | High degree of control | Very little control |
Chances of Error | Low | Very high |
Cost | Low for high volumes | Low for small volumes |
Compatibility | High | Low |
Component Density | High | Low |
Suitable for | High Volume Production | Low Volume Production |
Several types of electronic components are not compatible with the manual soldering process:
Large components with densely packed leads under their body, such as Ball Grid Arrays. As the pins are under the body of the component, they are inaccessible to manual soldering techniques, and automated reflow soldering is the only process to solder them effectively.
Quad flat packs or QFPs with fine pitch pins. As the pins are sensitive to co-planarity,some pins may remain above the pads, making them difficult to solder manually. In the automated soldering process, the pins will initially rest on soft solder paste, which will solder them easily.
Very small surface mount components, size 0201. These are too tiny to manually hold and solder in place, and require automated placement and soldering.
Automated soldering also allows close packing of components. Manual soldering requires adequate space between components to allow the introduction of the bit. With tightly packed components, it is difficult to manually solder them, as there is not enough room for the operator to place the parts and solder them.
However, under special circumstances, manual soldering scores above automated soldering. For instance,PCB prototyping services and small batches of board assemblies do not justify the time and expense necessary for programming and setting up an automated assembly line—assembling them manually is less expensive and faster.
Manual soldering may also be the last resort for components that have arrived after the majority has been soldered on the PCB.
Conclusion
Although automated soldering is the preferred process for assembling electronic circuit boards, there are times when the process requires a human touch, for touch-ups or for repairs and replacements. Most contract manufacturers have resources for both processes in place, and use them judiciously for achieving the best results